Testing tractors in a virtual environment
Manufacturers turn to computer technology to validate new machine designs
| 6 min read
By Scott Garvey
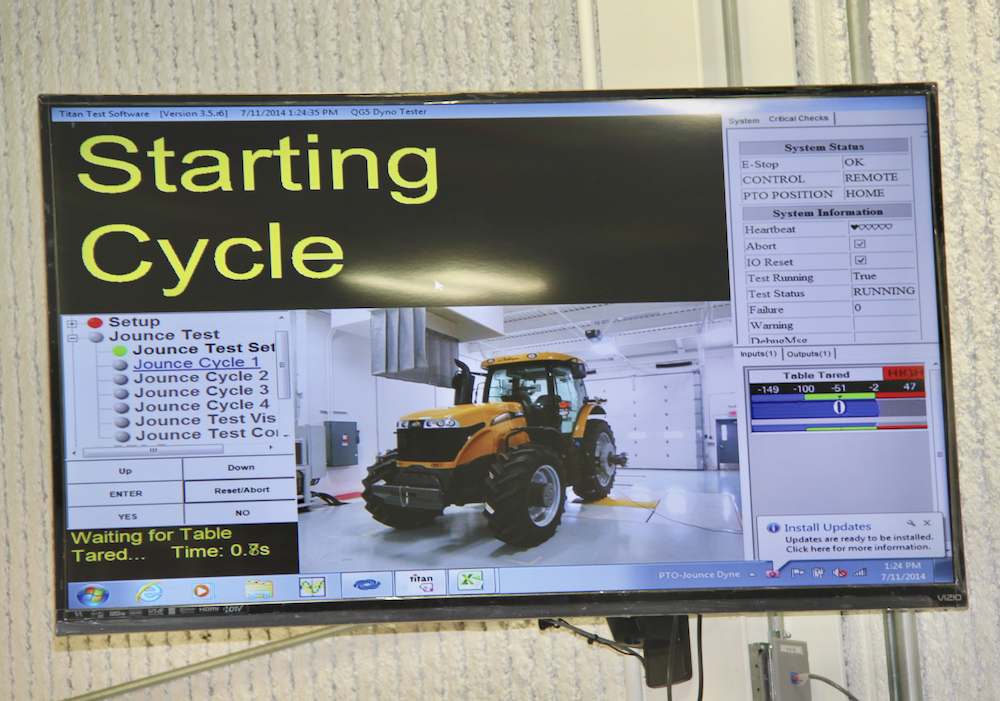
At AGCO’s Jackson, Minnesota assembly plant computerized jounce testing is used to look for assembly line defects before a tractor is shipped to a dealer. Photo: Scott Garvey
A few years ago I was interviewing a retired engineer who had worked at Massey Ferguson. We were talking about his involvement in testing prototypes, and he recalled how a group of employees would have to take shifts running newly designed machines over the “bump track” behind the engineering centre.
That was a track with concrete ridges designed to severely shake a machine as it drove over them. It could simulate years of real world experience in a week or two of 24-hour-a-day torture on the track. Unfortunately, it amounted to torture for the drivers as well.
That’s a pretty common testing procedure, and I’ve seen machines making the rounds on bump tracks in various test centres over the years. Driving around them for hours on end isn’t a job I’d be interested in. Fortunately, similar tests these days don’t actually require a driver.
One of the examples of a driverless bump track is in use at the DLG testing facility in Gross Umstadt, Germany. A rotating arm pulls a tractor around a circular track that resembles an exercise rack you might see at a horserace track. Staff can set the speed and duration of the test and control it remotely.
An even more modern version of the bump track is common in engineering centres such as CNH’s Burr Ridge facility in Illinois.
There, the tractor or other machine remains stationary with all four wheels securely positioned on top of fast-acting hydraulic rams that jostle it based on a computer program. When I went first toured the centre, CNH’s tests began with a real tractor travelling over a rough road at high speed with accelerometers recording the G forces. Those readings were then loaded into a program that used the rams to recreate the road inside the test chamber.
As I watched the test, I was asked not to photograph it because the test tractor was subjected to a merciless pounding. (Actually, it looked relatively unscathed at the end of the beating.)
Today the “jounce test” at AGCO’s assembly plant in Jackson, Minnesota, is far less severe and used as a quality control test instead, looking for potential assembly line faults such as poorly connected electrical fittings that might eventually bounce loose. That allows the defects to be corrected before the tractor gets shipped out to a customer.
Next door to the jounce test is a dyno room, where even belted tractors can get put through a series of gear changes and other driveline tests while under load. Again, this is meant as a non-destructive quality control test looking for assembly defects.
At the heart of these newer testing systems is, of course, computer control, something my retired Massey engineer friend couldn’t even have dreamt about during his work in the 1960s.
Then, earlier this year, CNH announced it has upped its game for testing new designs. There’s more to consider now than just the sore backs of test drivers. Test systems need to be safer too, and more environmentally friendly since all brands are under pressure to reduce their carbon footprints.
“Test-driving agricultural equipment must be conducted according to the most stringent safety conditions and in controlled scenarios,” says the company’s announcement. “Manoeuvering a 25-ton combine harvester across an uneven field can be a tricky business, so the greatest precautions and considerations must be made. CNH Industrial’s development of virtual testing is transforming that risk profile, as well as reducing the time, costs and carbon emissions involved.”
Another testing consideration is that the old school tests aren’t good enough these days. Today’s science has superseded it. Engineers now have practically unlimited data on soils and on field conditions and can predict the full range of stresses their machines will face.
And that can save a company a lot of dollars. No longer do they have to actually go through the expense of building a prototype to see how much abuse it can take before it breaks.
By testing in a virtual environment, CNH Industrial says it is speeding up the design process for full autonomy while minimizing occupational safety concerns.”
(Editorial note: Did anyone else notice the mention of testing for “full autonomy”?)
“One area where virtual testing is particularly effective is in cab design, where driver comfort and safety are assessed,” CNH adds. “By using virtual cabs, teams can closely monitor factors such as driver comfort and the reachability of controls. Whereas traditionally, a person would have had to physically sit in the cab for ergonomic testing — possibly in some potential discomfort — the virtual system can assess all the design factors.”
Virtual testing also allows customers to provide input and feedback into the design process, the company says. “Using virtual cabs, they can view solutions, track design development, and see improvements to product design first-hand interface and advanced sensing technology that allow the vehicles to locate themselves and avoid hazards. However, the next step forward is already with us: supervised autonomy, where the operator oversees an unmanned vehicle. Ultimately, CNH Industrial will deliver full autonomy, where farming machinery will be able to carry out a wide range of tasks under fully remote supervision.”
Virtual tests can be designed to focus on any number of aspects, including safety as engineers refine the design through the development process.
“Normally, the product development team would run a series of ‘bump tests’ for farming equipment, which monitors vibrations, analyzes the forces on specific elements of a design, and checks the pressures on hydraulic components,” the CNH explanation continues. “But now, by combining a variety of modelling techniques with physical components, CNH Industrial has created a simulation environment that mirrors standard testing, creating a ‘digital twin’. By shifting to this virtual setting, design validation becomes far safer.”
In order to compete in a wide range of global markets, traditional testing requires farm equipment to be evaluated in different environments and crops. Virtual testing speeds that process up too.
Not surprisingly, any process that gets a machine from concept through development and into commercial sales faster can save companies a pile of cash. By running a virtual test, evaluations are effectively immediate. And CNH notes it is also possible to learn more about the machine’s operation than during standard physical testing.
Not only that, but the computers can “see” every phase of the operation as well, such as the insides of a combine rotor that is full of crop.
“With these simulations we can analyze the dynamics of all the systems inside the machine,” CNH says. “The company’s ability to monitor the exact crop flow at every point inside a virtual machine makes testing more accurate and allows for further enhancements.”
And then there’s that environmental angle. Testing vehicles in the traditional manner involves significant carbon emissions — and waste. Running virtual simulation substantially reduces those concerns.
“When building a prototype, you know it is ultimately destined for the landfill,” says Gennaro Monacelli, CNH Industrial’s global director of design analysis and simulation. “It’s a significant investment and thanks to virtual testing, we don’t always need to develop one, as simulations become more realistic and predictive.”
Besides, there are whole new systems that need testing under every kind of condition, including cameras and LiDAR (Light Detection and Ranging), in everything from clear sunny days to rain storms. The old bump track doesn’t offer much help there.
“On larger farms, vehicles will soon be able to communicate with each other,” says Monacelli. “In the future, we will be able to tell farmers the optimum time to harvest a crop, and the combine will harvest with fully remote supervision.”
– This article was originally published in the November 2022 issue of Country Guide.