Are vertical farming operations here to stay?
| 9 min read
By Don Norman
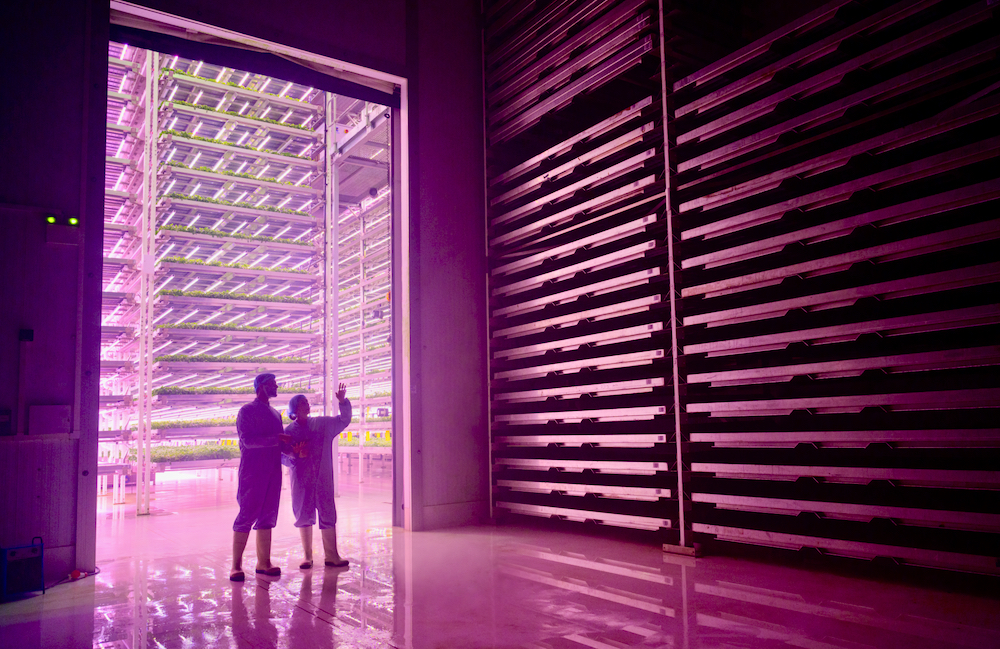
“You can take the same set of genetics and apply a different environment, and that plant will be different; it will taste different; it will look different and it will have a different nutritional fingerprint.” – Thomas Graham, University of Guelph. Photo: JohnnyGreigiStock/Getty Images
Broadly speaking, commercial vertical farming operations are humankind’s attempt to grow food under conditions more controllable than Mother Nature allows and with a minimum of wasted space.
Many seem like sci-fi greenhouses: hydroponics, plants growing in stacks or up walls and high-tech sensor setups that seem straight out of the mind of Gene Roddenberry.
And, with an increasing number of companies trying to make a go of it in Canada, vertical farming has become a buzzword.
“Vertical farming is too broad of a term, in my opinion,” said Thomas Graham, assistant professor and PhytoGro research chair in controlled environment systems at the University of Guelph. “When I say vertical farming, I’m talking about stacked multi-layer production systems, or plant factories.”
Beyond the ability to control light and temperature, the production system has made waves as a system in which pests and pathogens can be eliminated, chemical input costs shortened considerably and the risk of contamination can be limited. Lettuce, for example, is a common product for vertical operations. It is also a product at the heart of several salmonella scares.
In terms of medicinal crops and plant-based pharmaceuticals, the controlled environment of vertical farms is ideal.
“If you take those plants that are making a drug [compound] and grow them in different environments, a drug could be different. So you need to give it the same conditions 365 days a year. You can only do that indoors,” Graham said.
It is unrealistic to imagine a future where vertical farming replaces ag as we know it, he added, but it can be seen as complementary to field production.
“It’s just another piece of the food supply puzzle that is getting more and more complex.”
Setting the seed
Vertical production, like all greenhouses, comes down to lighting. But while greenhouses let in light and trap heat, they are still dependent on sunlight and susceptible to cold weather. Vertical operations don’t leave those variables up to chance.
The history of grow lighting stretches back for decades. The 70 years after the invention of the electric light bulb in 1879 saw a steady stream of improvements that helped develop lighting for plant growth. By the 1960s, metal halide and high-pressure sodium lamps had emerged in the horticultural sphere. Greenhouses could now supplement their lighting to extend the growing season and, today, even run year-round with the help of other advances, like insulating energy curtains.
“You can do indoor farming in just a single layer with a fairly high roof using these high-pressure sodium [or] metal halide lights,” said Graham.
Many cannabis farms use this technique.
Building up
To shrink the historically sprawling footprint of a greenhouse and make farming stackable, more advanced lighting was needed. Metal halide lights, for example, tend to throw off a lot of heat, Graham noted.
In a regular greenhouse, that can be an advantage if the facility can capture the heat load and use it to regulate winter temperatures. In a vertical operation, where lighting is typically much closer to foliage and produce, it becomes a problem.
“They’re good lights, but they’re really hot,” Graham said. “You can’t get too close.”
Advances in LED lighting, which run much cooler, would eventually solve that problem. The first LED lights were invented in 1958, but it would take decades for them become useful horticulturally.
“The use of LEDs for horticultural lighting actually started in the space program, with some NASA grants,” said Graham. “Up to that point, they weren’t all that efficient.”
LED advancements began to take off in the early 2010s. As they evolved, so did their promise as a horticultural light source.
These lights have fairly narrow wave bands, allowing generation of different colours. This allowed NASA researchers to identify the parts of the spectrum (red and blue light) that plants best absorb.
“Their reasoning was to use what chlorophyll absorbs best so as not to waste photons on things the plant isn’t using,” said Graham. “That’s why, on a lot of these farms, you’ll see this kind of really annoying magenta light.”
As LEDs became more efficient, the understanding of a plant’s relationship with light also evolved. Other colours on the spectrum were found to play roles in plant development.
“LEDs have allowed us to start to play with the colour of light that we apply to a plant, and that is profoundly impactful,” said Graham. “You can take the same set of genetics and apply a different environment and that plant will be different. It will taste different, it will look different and it will have a different nutritional fingerprint.”
That’s highlighted in a recent Agriculture and Agri-Food Canada study. The study looked at different combinations of red, blue and amber LED lights to see how they affect the production of carotenoids (antioxidant pigments) in brassica microgreens.
The study discovered that when amber-blue light was increased and red light was decreased, carotenoid content rose significantly.
The spread of vertical farming
Visitors to Canada’s circuit of agricultural trade shows will have seen a number of booths devoted to vertical farming. Others have been highlighted in media reports.
One such company, which participated in the 2023 Manitoba Ag Days Innovation Showcase, has put down roots outside Winnipeg.
Harvest Today Canada uses what it describes as “vertigation,” a wall of soil-filled peat cups, vertically irrigated and formed with interlocking modules reminiscent of Lego blocks.
As of January, the company was operating a 720-plant wall at its Winnipeg facility, but was also selling the technology to communities looking to set up their own plant walls. They had an international customer list, and had flagged the potential for remote communities such as Canada’s North.
In Ottawa, a company called Growcer is using stacked growing systems under LED lighting. Company co-founder Alida Burke was inspired to enter the vertical farming marketplace after a trip to Iqaluit in 2015.
The company began using shipping containers to house its hydroponic operation, but soon discovered space limitations. Now it houses its farms in 40-foot insulated modular containers and operates more than 70 farms across Canada.
Another incoming enterprise hopes to refurbish the long-empty McKenzie Seeds building in downtown Brandon. According to local media reports, Brandon Fresh Farms is investing $30 million to retrofit the 120,000-square-foot heritage building into a massive vertical farm.
Early estimates suggest that farm will be able to grow 180 tonnes of food per month. Construction is slated for early in the New Year and the company hopes to produce vegetables by 2025.
“The potential is there for some real contributions to things like food insecurity in urban or northern remote communities,” said Graham. “I think that this upswell of optimism about the technology and this realization that we can grow food right beside us indoors all fit into that.”
Bursting the bandwagon bubble
It’s not all good news.
In July, McGill University bioresource engineering professor Mark Lefsrud noted headwinds facing the sector. He was quoted as part of a BBC article titled “Lean times hit the vertical farming business.”
The article noted vertical farms that have hit stumbling blocks, such as U.S.-based AeroFarms, which filed for bankruptcy protection this summer. One French company has gone into receivership, BBC reported, while other U.S. companies have laid off staff.
A release by McGill University said European vertical farming company Infarm has changed its focus from Europe to “regions with lower energy costs.”
“This shift signifies the challenges in maintaining profitability while keeping sustainability promises,” the release noted. “Vertical farming stands at a critical juncture, with its promise and potential weighed against the realities of implementation.”
Infarm’s shift was also noted by the BBC.
Graham thinks the wheat has mostly been separated from the chaff by now.
“The majority of those farms were started by people who had no agricultural background whatsoever,” he said. “They loved the idea, they were sold on it, and they threw a bunch of money at it. That was one issue.”
Another issue was the industry-spanning shipping container craze, said Graham. Many indoor farming businesses were seduced by the sturdy, relatively cheap structures, but they proved to be less of a boon than many hoped.
“In limited circumstances, shipping containers can be effective, but generally they aren’t,” said Graham. You don’t get the economies of scale.”
Finally, there’s the bandwagon effect.
“It’s the same with any nascent industry. You get that bubble, and that bubble has burst,” said Graham. “The good ones are surviving, and they’re making profits now.”
Lessons learned
As the industry matures, Graham says the lessons learned from early startups can be helpful for today’s entrepreneurs.
For instance, Olds College in Alberta is launching an indoor agriculture certificate program next fall. It’s the first of its kind in Canada and Jay Steeves, dean of the college’s Werklund School of Agriculture Technology and one of the program’s developers, has noted the interest.
“We did a feasibility study at the college and there’s probably about 50 or 60 different corporations around the area that are dabbling in this and would love to have more people with a skill set kind across that entire spectrum,” he said.
The sky isn’t the limit; energy is
Energy is still a major limiting factor for vertical farming. Even with new, efficient LEDs, any large-scale, intensive operation will require a lot of power.
“The vertical farming sector right now is at a point where leafy greens, baby greens, microgreens, et cetera, are all certainly economically feasible right now, and a good number of the farms are actually finally making money with those crops,” said Graham. “But you’re never going to feed the world on lettuce.”
Those types of crops offer a quick turnaround, limiting the energy dollars that go into each unit sold.
Harvest Today started with greens and herbs, but as of Ag Days in January, was developing the technology to expand into flowering plants like tomatoes, peppers and cucumbers.
Graham also noted the work being done now to develop the production system for higher-caloric crops, or crops with higher fibre or protein. There, plant breeding will have to keep up.
“You can breed shorter crops, so you can squeeze more in,” he said. “You can also make more of the plant edible.”
Plants could also be bred to have lower light requirements, he said.
“Let’s be realistic. There will always be field agriculture. There will always be greenhouses. This is just the next technologically advanced step.”